Single Deep, Double Deep, or Multiple Deep Storage - How to Decide?
Gary . • 4 August 2023
Single Deep, Double Deep, or Multiple Deep Storage - How to Decide?
When designing a new warehouse storage system, it is important to fully understand the business operations and inventory of products that need to be stored, while focusing on productivity and space optimization. There are several types of storage systems, single selective, double-deep and multiple-deep. Each of these systems provides distinct benefits and considerations that Checkpoint Group will analyze along and collaborate on to ensure that the system design is fully optimized for the business’s operational needs. Checkpoint Group have a wealth of experience and are excited to share our expertise in designing, supplying and integrating all types of warehouse systems.
Exploring Different Types of Systems
a) Single Deep Storage System: With this type of design, each pallet is stored in its own dedicated location providing 100% selectivity at all times with fast and easy access - perfect for warehouses with an array of SKUs that require frequent picking/replenishment operations as is a popular choice in most applications.
b)
Double Deep Storage System: This configuration increases storage density, where two pallets are stored one behind another on pallet racking. A double-deep system is best-suited when the operation has quantities of each SKU. In a double deep system, FILO (First In Last Out) is how products are usually picked. Applications where expiry dates are important provide an additional layer of consideration. When picking loads, this can be done using a double-deep forklift fitted with either a pantograph reach carriage or hydraulically extendable forks. A double-deep system can also be configured with pushback carts and will allow the use of a conventional forklift, as the carts will bring the back location to the front using gravity.
c)
Multiple Deep Storage System (Pushback or Pallet Flow): In multiple deep systems (Pushback Carts or Pallet Flow Rails) are the most common choice. In this configuration, multiple pallets are stored one behind the other in lanes.
Push Back System: First In Last Out (FILO) uses mechanical carts and gravity, loaded from the front and picked from the front. This system only requires an aisle at the front, providing a smaller footprint than a pallet flow system.
Pallet Flow System: First in First Out (FIFO) uses mechanical rails and gravity, loaded from the back and picked from the front. One minor downside is that this system needs an aisle at the front and the back of the system – increasing the required footprint for the same number of pallets.
Depending on how the operation requires products to be picked (FILO or FIFO) is often the leading indicator of which system is to be considered first.
Density and Aisle Space
Choosing the right system comes with a trade off in all cases, it is Checkpoints responsibility to analyze all of the factors within the operation to best determine the most optimal system and provide a recommendation that optimizes both the system and the efficiency.
Single Deep = Maximum Selectivity, with the Minimal Density and largest sq/ft per pallet ratio.
Double Deep = Moderate Selectivity (50%), Increased Density and better sq/ft per pallet ratio.
Multiple Deep = Lowest Selectivity, Highest Density and smallest sq/ft per pallet ratio.
Checkpoint strongly supports the study of all aspects within the operation to ensure that there is no wasted space.
SKU versus Volume Considerations
Understanding your SKU-volume dynamics is of utmost importance when selecting a storage system. Single deep systems are best suited when managing high numbers of SKUs and inconsistency due to their 100% selectivity and thus are also suitable for frequent order picking operations.
Double-deep systems are best suited with a mix between High-SKU and Quantities of each SKU, where having the same product stored one behind the other.
Multiple deep systems work best when handling items with few SKUs that require accessing pallets in volume, ideally when they are all the same going on the same trailer.
Importance of Selectivity
Selectivity refers to the ease of retrieving specific items from storage. While density is important, having an order fulfillment and inventory management system with optimal selectivity will prove beneficial for businesses that rely heavily on frequent picking activities and have multiple product ranges to manage. Single deep systems offer optimal selectivity versus the other system designs.
Selectivity is less of an important factor when shipping many types of the same SKU at once.
Future Outlook of the Narrow Aisle Market
The narrow aisle market is projected to experience substantial expansion over the coming years, thanks to advances in technology like articulated forklifts and turret trucks which have revolutionized narrow aisle operations by providing enhanced maneuverability that maximizes space utilization while improving productivity in narrow aisle environments. Adoption of such innovative solutions by warehouses across both Canada and USA should increase as they strive for greater efficiency while cutting cost of operations.
Narrow aisle equipment paired with the correct choice of storage system configuration will provide business’s with a highly effective inventory management process.
Checkpoint Group's Design, Supply, and Integration Services
At Checkpoint Group, we specialize in offering comprehensive design, supply and integration services for various storage systems across Canada & USA. Our knowledgeable team works closely with each of our clients to understand their unique requirements and optimize warehouse operations - be it single deep, double deep or multiple deep systems - providing tailored solutions that maximize space utilization while improving selectivity and overall efficiency.
In addition, our wealth of experience with many brands of material handling equipment can provide insightful perspectives in a highly effective strategy towards a common optimal goal…
As businesses seek the optimal
storage solutions, implementing single deep, double deep or multiple deep systems requires careful consideration of factors like density, selectivity, SKU versus volume dynamics and future market trends. Checkpoint Group provides design, supply and integration services so businesses can make informed decisions with high returns on investments by choosing an ideal storage system - including improved efficiency through optimized space utilization as well as faster picking processes.
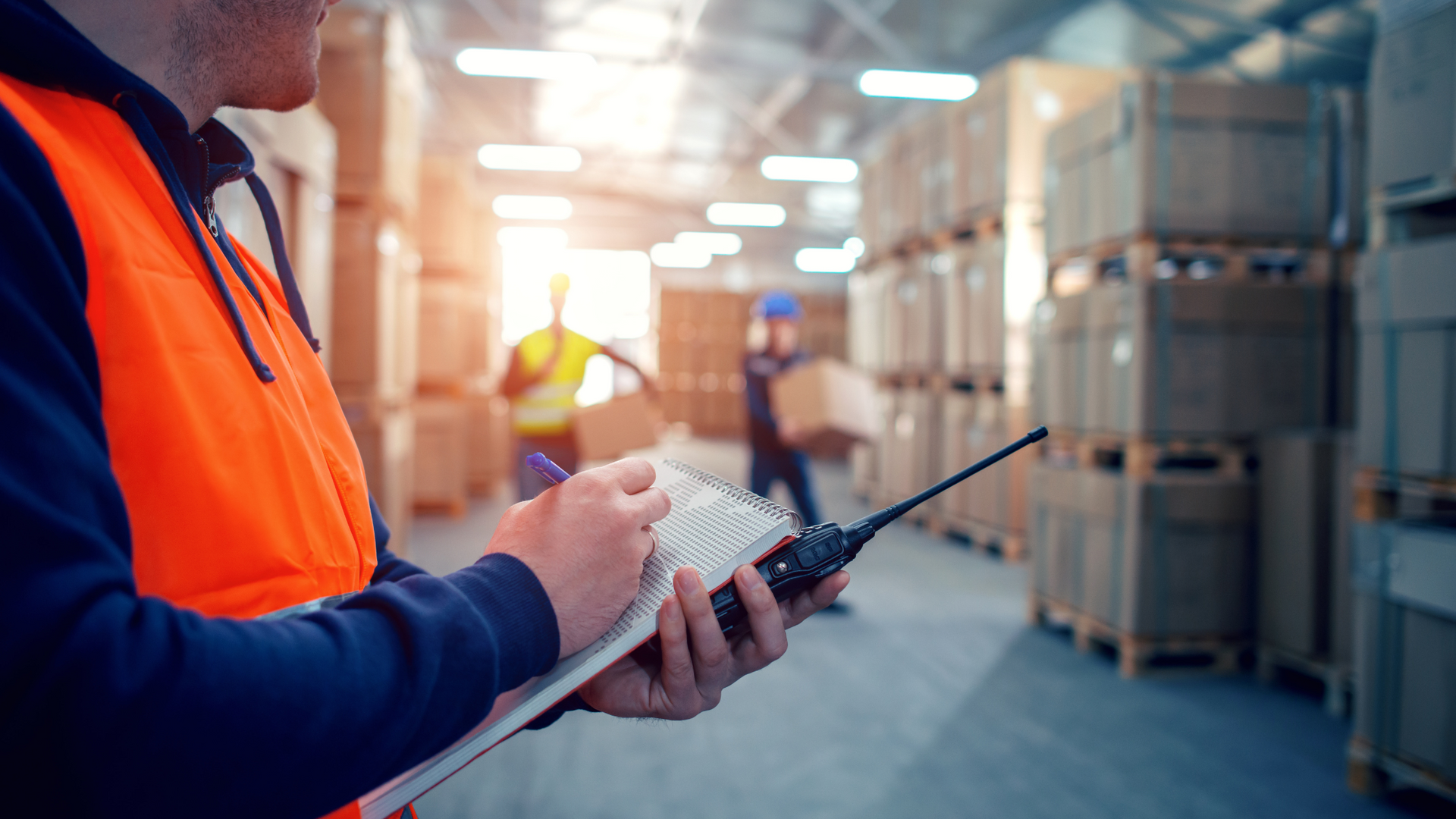
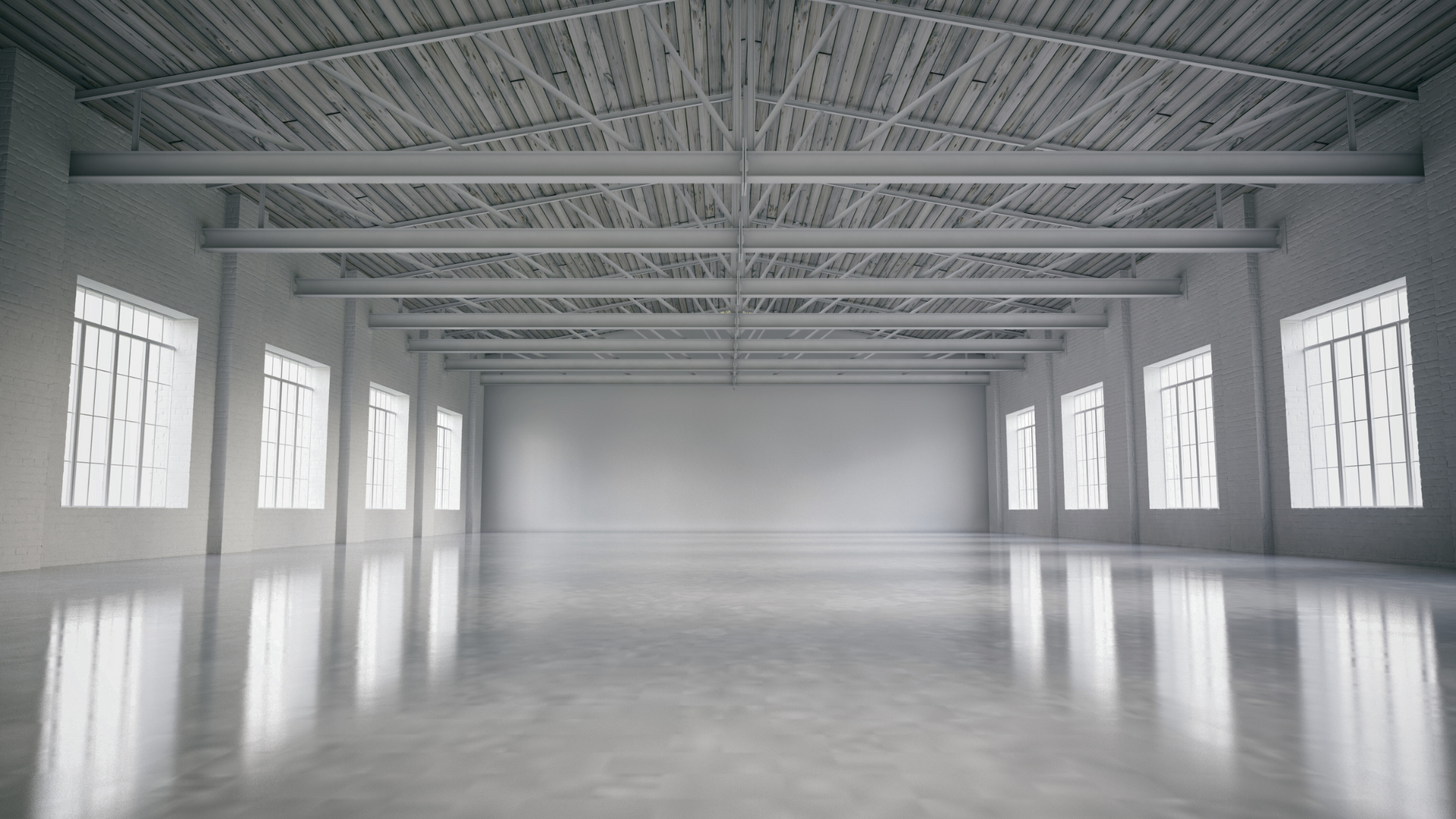
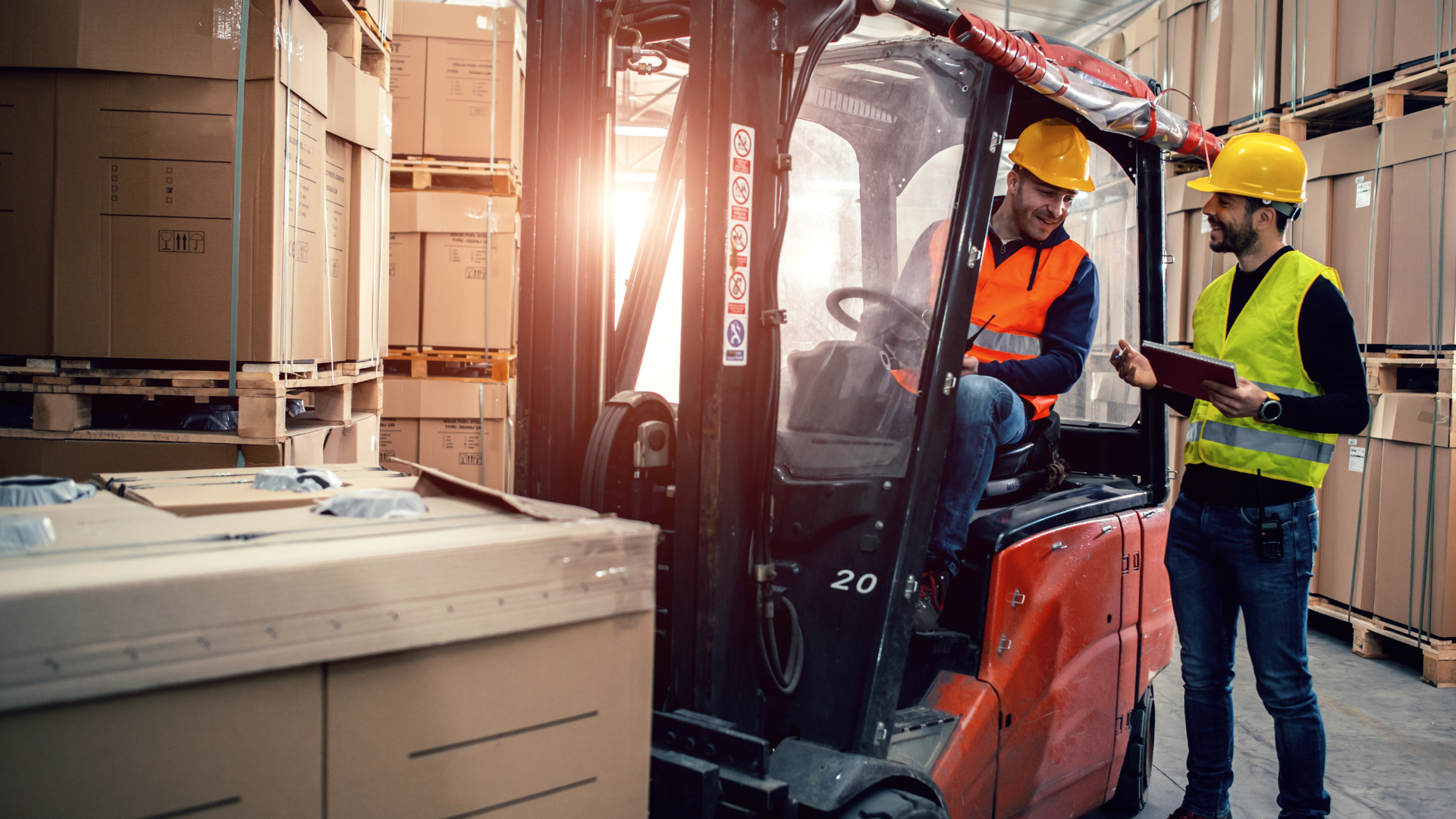